How to exam and repair biomass pellet machine?
After running for a period, the wood pellet machines are likely to have some problems due to dust pollution and insufficient maintenance. A pellet machine engineer said: “Most pellet machine failures are caused by improper operation, not the quality problem of the machine.”
Wood pellet production can be divided into 5 elements: pellet machine, pellet machine operator, raw materials for making pellets, the method to make pellets, and the production environment. Therefore, when faced with problems, you can find reasons from the 5 aspects.
When do you need to repair the wood pellet machine?
Before the pellet machine break down, there are usually some symptoms. You can avoid pellet machine failures by paying attention to these symptoms.
Pellet mills have abnormal sound from inside
This condition means there are foreign matters getting into the compression chamber, such as screws, and iron nail. They will be stuck at the holes of the die. When the roller press over them, they will cause abnormal sound.
Foreign matters in the compression chamber do great harm to the roller and die. If this happens, you must stop the machine at once, and clear away the foreign matters in the die. To avoid this condition, you can remove the iron object with a magnetic separator before feeding them into pellet machine.
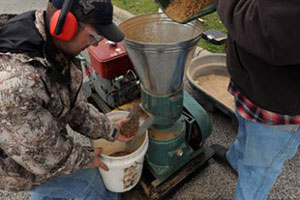
The pellet mill die get blocked and no pellets come out
This is usually because the raw materials has over-high moisture content. Under this condition, the pellet machine runs in high capacity. The roller and die will slip. When the raw materials become paste, they would block the die holes. So it is recommend to keep the moisture content of raw materials between 15%-20%.
If the moisture content is higher than the requirement. We need to dry off the materials with a dryer machine or in the sun, or they would affect the production efficiency and shorten the working life of pellet mill.
Besides, if the raw material layer between the roller and die is too thick, the die holes will also get blocked. Under this condition, you need to shut down the pellet machine, clear out the materials in the compression chamber, and adjust the clearance between roller and die.
Automatic lubricating oil pump alarm
The environment for wood pellet production is often filled with ash and dust. When the dust get into the self-lubricating system, it will cause oil-line plugging. When the inner pressure run up to certain limit, the lubricating system will alarm.
Some operators would ignore the abnormality in the lubricating oil pump, so that the bearings can’t get lubricated in time, which will cause serious damage to the pellet machine.
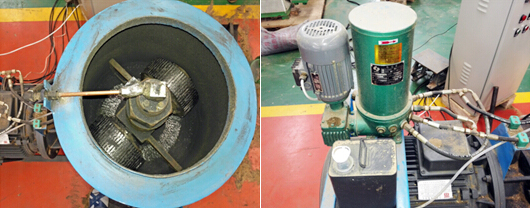
Pellet machine lubricating system
The wood pellet production become too low
Wood pellet machine adopts the pressure and fraction from the pellet mill die and roller to biomass pellets. Pellet mill die and roller are the wearing parts. They can last 800-1000 hours. If the raw materials have high hardness and granularity, they would intensify the abrasion of the wearing parts.
If the roller and die wears out, the production will decrease, and the forming rate will be low. Under this condition, you need to disassemble the pellet machine and replace the wearing parts. Besides, the bearings and transmission shafts are also wearing parts. If they wear severely, they will also affect the production and even cause the machine to break down.
How to repair the biomass pellet machine properly?
Exam the wearing parts of pellet machine regularly. If there are blockage, low production or low forming rate, they usually arise from the wear of roller and die. Replace the worn spare parts in time to ensure continuous work of the pellet machine.
To ensure safety, you must cut off the power before removing the cover, then you can touch the roller and die with your hand or tools.
To replace the pellet mill die, you need to take down the press roller and slicer at first, and screw off the cap on the spindle, then you can take down the die and replace for a new one.
After replacing the pellet machine, make sure the rotating direction of the die in accord with the sign on the machine. Loose the 2 adjusting screw on 2 sides of the roller, so that the machine start to run in zero load.
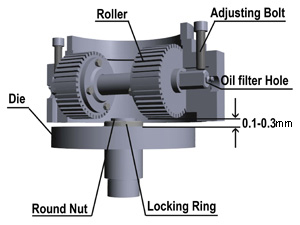
Pay attention to the automatic oiling time, volume and uniformity. The molding of biomass pellets requires high temperature. Timely oiling and heat dissipation can ensure continuous production, and prolong the working life of roller and bearings.
During high load production, keep an eye on the electricity, sound, dust, wood pellet status, and oiling amount. Diagnose the problems according to the specific situation, and take effective measures.
Biomass pellet machine need all-round maintenance after every half a year. Add high-heat oil to the transmission shafts and bearings.
We receive enquiries in English, Español (Spanish), Русский язык (Russian), Français (French) and العربية (Arabic). Our professional team will reply to you within one business day. Please feel free to contact us!