What are the parts of a flat die pellet mill?
Flat die pellet mills are popular biomass molding equipment for their high convenience and low cost. Compared with ring die pellet mill, it features small volume, simple design and low capacity, so it is suitable for home use and small-scale production.
It can form sawdust, crop straw, rice husk, bark, grass and other biomass materials into high-density pellets, so they are convenient for storage and transportation. These biomass pellets are widely applied in home heating and power generation as an substitute for coal, oil and gas, for they are clean and renewable.
Constituent part of a flat die pellet mill
Flat die pellet mill is mainly composed of 3 parts: pelletizing part, drive engine and drive system. To be specific, a flat die pellet mill is constituted by a feed hopper, upper box body, adjusting nut, pellet outlet, spindle box, gear box, transmission shaft, foundation, wheels, electric motor, electric control cabinet. Meanwhile, the electric motor can be replaced by diesel engine, gasoline engine and PTO connector.
Gemco flat die pellet mills can be classified into roller-turned type and die-turned type. The former one works as the roller rotates and the flat die keep still, while the latter one works as the roller keep still and flat die rotates. Both of them are able to make qualified wood pellets. But R-type adopts smarter structure and superior gearbox, so it has higher power and capacity, and the cost is higher, too.
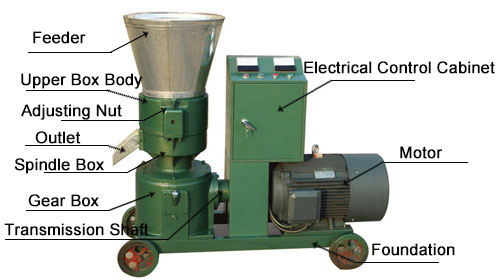
Die-turned pellet mill constituent parts
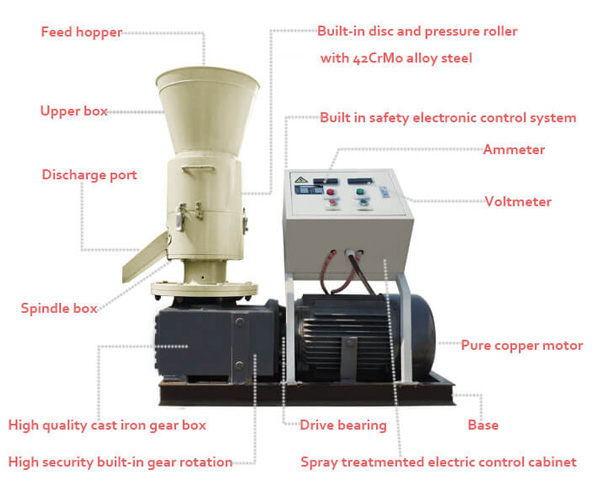
Roller-turned pellet mill constituent parts
The components of Die-turned flat die pellet mill
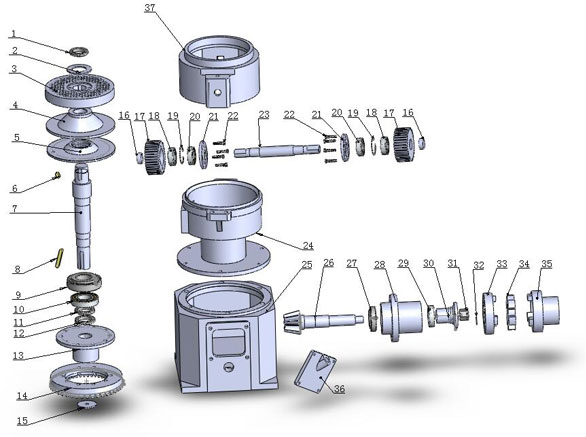
No. | Name | Qty | No. | Name | Qty |
1 | Round Nut | 1 | 20 | Bearing | 2 |
2 | Flat Washer | 1 | 21 | Bearing Cover of Roller | 2 |
3 | Die | 1 | 22 | Hex Bolt | 8 |
4 | Disc of Throwing Pellets | 1 | 23 | Roller Shaft | 1 |
5 | Dust Cover of Main Shaft | 1 | 24 | Shaft Box | 1 |
6 | Flat Key of Type A | 1 | 25 | Gear Box | 1 |
7 | Main Shaft | 1 | 26 | Gear Shaft | 1 |
8 | Flat Key | 1 | 27 | Bearing | 1 |
9,10 | Bearing | 1 | 28 | Pinion Seat | 1 |
11 | Round Nut | 1 | 29 | Bearing | 1 |
12 | Round Nut | 1 | 30 | Splined Sleeve | 1 |
13 | Big Gear Seat | 1 | 31 | Castle Nut | 1 |
14 | Big Gear | 1 | 32 | Cotter Pin | 1 |
15 | Washer | 1 | 33 | Passive Coupling | 1 |
16 | Check Ring | 2 | 34 | Elastic Washer | 1 |
17 | Roller | 2 | 35 | Active Coupling | 1 |
18 | Bearing | 2 | 36 | Cover of Observation Hole | 1 |
19 | Washer | 2 | 37 | Upper Box Body | 1 |
The components of Roller-turned flat die pellet mill
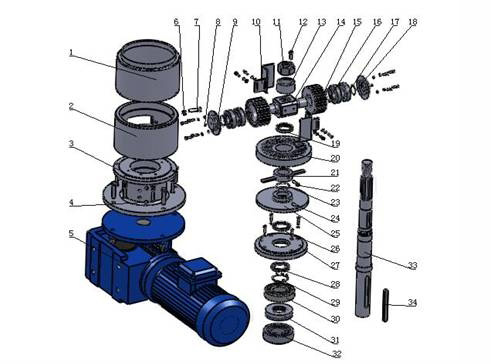
No. | Name | Qty | No. | Name | Qty |
1 | Upper Box Body | 1 | 18 | Check Ring | 2 |
2 | Shaft Box | 1 | 19 | Grease Seal | 1 |
3 | Bearing Seat | 1 | 20 | Die | 1 |
4 | Straight-through Oil Cup | 2 | 21 | Cutter | 1 |
5 | Reducer | 1 | 22 | Hex Bolt | 1 |
6 | Hex Nut | 1 | 23 | O Shape Seal Ring | 1 |
7 | Hex Bolt | 1 | 24 | Disc of Throwing Pellets | 1 |
8 | Pressure Oil Cup | 2 | 25 | Hex Bolt | 1 |
9 | Cover of Roller | 2 | 26 | Grease Seal | 1 |
10 | Discharge Scraper | 2 | 27 | Dust Cover of Shaft | 1 |
11 | Hex Bolt | 1 | 28 | Round Nut | 1 |
12 | Nut | 1 | 29 | Lock Ring | 1 |
13 | Washer | 1 | 30 | Bearing | 1 |
14 | Roller Shaft | 1 | 31 | Grease Seal | 1 |
15 | Roller | 2 | 32 | Bearing | 1 |
16 | Felt | 2 | 33 | Main Shaft | 1 |
17 | Cylindrical Roller Bearing | 4 | 34 | Flat Key | 8 |
How does a flat die pellet mill work?
When you start the flat die pellet mill, the electric motor rotates and bring along the main shaft through the transmission shaft and gearbox. The roller is connected with the main shaft, so it revolves around both the main shaft and its own axis.
When you feed raw materials into the hopper of pellet mill, they fall on and spread over the flat die evenly. Under the drive of main shaft, the roller rolls over the raw materials continuously, and press them into the holes on flat die. The materials get formed and solidified in these holes, and come out in the shape of cylinders. Under the flat die, there are slicers cutting the pellets into certain length. The cut pellets fall on the pellet throwing disc and get out through the outlet.
During the operation of pellet mill, the relative motion of roller and die heat up the raw materials and press them into the holes on flat die. The roller is driven by the main shaft, the shaft is driven by the gearbox, and the gearbox is driven by the electric motor.
Roller and flat die: the core part of a pellet mill
The core par of flat die pellet mill is a disc flat die with multiple holes and a roller with slots on the surface. The flat die is made of ductile cast iron, the thickness, hole size and quantity have huge effect on the production quality and capacity. You can make pellets of different diameters with flat die of different hole sizes.
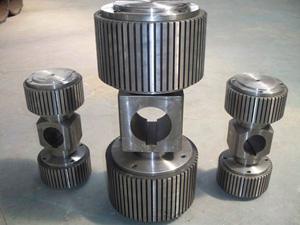
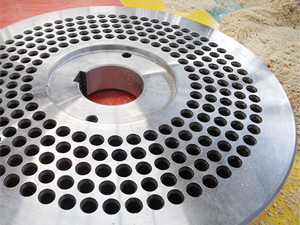
The roller is made of superior alloy steel. Its hardness is 55-60HRC, lower than that of flat die so as to prolong the working life of flat die. The roller is installed on a roller shaft which it also rotates around. The larger the diameter of roller, the larger the grabbing force it has on the raw materials. Meanwhile, the materials layer can be thicker to improve the production. The roller shaft has two roller on both ends, their clearance with the flat die should be the same.
The roller has skid-proof tooth ace on its surface. Under the pressure of two roller and the shaft box, raw materials are distributed on the flat die and two rollers evenly. When the roller rotates driven by the main shaft, the roller revolve on its own axis under the fraction with the raw materials. Therefore, they form strong pressure on tangent plane between roller and flat die and press the materials into the vertical holes on the flat die. As the roller repeatedly press over the raw materials, the length of the formed pellets accumulate and extend outward from the holes. The extended pellets will be cut into certain length by a slicer.
The features of flat die pellet mill design
- The roller of flat die pellet mill adopts tapered structure. So the rotating speed on the two ends are the same. This design avoid the friction caused by dislocation, reduce the waste of energy, and prolong the working life of flat die.
- The flat die pellet mill adopts screw central pressure adjustment device. You can change the clearance between roller and flat die to adapt to different materials so as to ensure the pelletizing effect.
- Gemco pellet mill adopts large-size and wide-slot rollers. They are durable with high loading capacity. To match up with the roller, the bearings are also enhanced with higher capacity. In this way, we prolong the working life of rollers bearings and reduce the production cost.
- The hole sizes of flat die are from 2.5mm to 10mm, and the 6mm, 8mm and 10mm are the most popular. They apply to different types of materials. Meanwhile, we achieved the best compression ratio by a multitude of experiments, so as to ensure the pelletizing effect.
- The machine body is cast in block, equipped with reinforce rib on the shell. It is sturdy with little possibility of fracture.
We receive enquiries in English, Español (Spanish), Русский язык (Russian), Français (French) and العربية (Arabic). Our professional team will reply to you within one business day. Please feel free to contact us!