How to choose and maintain the ring d
Ring die is the core part of a ring die pellet machine. It has great impact on the wood pellet production, power consumption and forming rate. A high quality ring die is the premise of continuous and steady production.
Ring die is an wearing part in the pellet machine. According to statics, its cost of wear and tear takes up 30% of the entire workshop. Therefore, to choose, use and maintain the ring die properly is important to a wood pellet manufacturer.
How to choose a suitable ring die?
Choose the compression ratio best for your materials. Compression ratio refers to the ratio of the hole length to the diameter. As the diagram below shows:
Make clear what materials and heat treatment it adopt. Ring dies are usually made of Carbon structural steel, alloy structural steel, stainless steel and processed by forging and stamping, lathe process, drilling and heat treatment, etc. Every process affect the working life, production capacity and quality of the ring die. Currently, the most popular material for ring die is 4Cr13, whose hardness can reach up to over HRC 50.
Observe the roughness of the ring die holes. If the inside of the die holes is too rough, it will affect the molding of pellets, and even cause blocking and plugging of the machine. If there are barbs inside the die holes, you need to grind it with a drill.
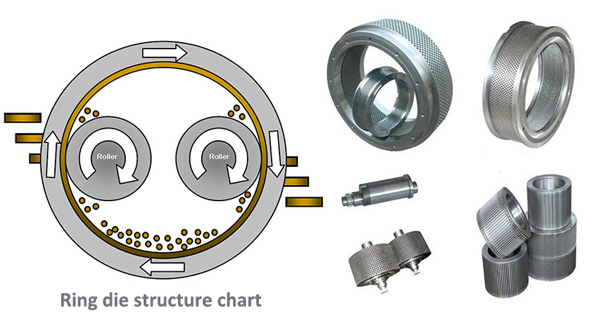
Specifications of the ring die holes
On the premise of high quality of ring dies, choose suitable die hole shape, opening percentage, and compression ratio. Generally, straight holes and stepped holes are suitable for making mixed feed, while outer-cone holes are suitable for high-fiber feed like skim bran, and inner-cone holes are suitable for light materials like grass powders.
High opening percentage can increase the wood pellet production, but it may reduce the ring die strength. To achieve certain compression ratio, some ring dies may be too thin and easy to break. To prevent this condition, we can increase its thickness and open pressure relief vent without increasing the effective length of the hole.
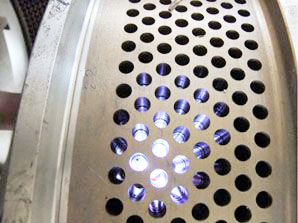
How to maintain ring dies?
Adjust the clearance between the roller and ring die
The clearance between roller and ring die have great impact on the production. The suitable clearance between the roller and ring die is 0.1-0.3. It means when you rotate the ring die with your hands, the roller is in a state between rotation and still.
After you have installed the ring die. Loose the adjusting bolt to let the outside of the roller stick to the inside of the ring die.
Then adjust the eccentric roller shaft to make every sides have the same distance from the ring die. Preload the adjusting bolts, pull the ring die, adjust the bolts slowly until the roller is in the state between rotation and still, then you can fasten the adjusting bolts.
When installing a new ring die, keep the clearance between the roller and die larger than normal, so that the new ring die break in well with the old roller. After the breaking-in period, you can reduce the clearance as you need.
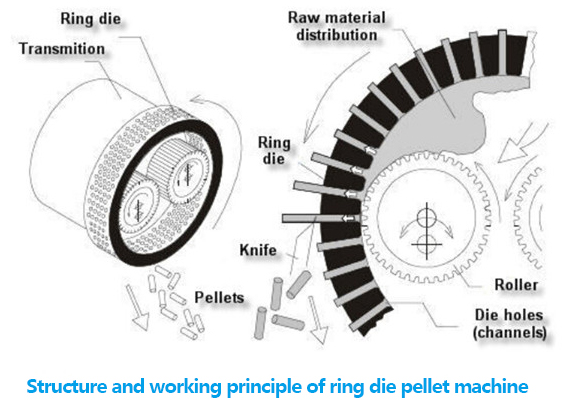
Protect the ring die in installation and production
When installing or replacing ring dies, especially from the cone side, prevent bruises or scrapes from the cone. Clean and lubricate the conical surface and the driving wheel rim cone if necessary.
If you want to disassemble the ring die, fill the hot oil materials into the holes of ring die, so that it can retain the best condition the next time it is used.
When using ring die pellet machine, we’d rather sacrifice the roller and protect the ring die, for the price of ring die is more than a dozen times of roller. Therefore, the hardness and abrasion resistance of rollers should be no higher than the ring die.
To ensure the productivity of ring die, regular maintenance is important. During wood pellet production, the ring dies usually have blocking, wear, seal, and internal turnover problems. They will cause the production drop and the power consumption rise. If the ring dies have such problems, you need to grind the inner side and chamfer.
Inspect the weariness of ring dies
For pellet machines who need to replace the ring dies frequently, check the driving wheel rim regularly to prevent the breakage of die centering pin resulting from excessive wear.
Excessive wear will affect the fit between the ring die and the wheel rim. If they don't fit tightly, the ring die would generate shear force to the centering pin and cause breakage. So if the centering pine breaks, it usually results from excessive wear of the drive wheel rather than the inadequate strength of the pin.
For ring dies assembled in hoops, check the assembly surface and matching components. After running for a period, the abrasion of the components will affect the matching precision, and cause the production drop. Then you should repair or replace to new components.
In conclusion, only choosing a suitable type of ring die and inspect and maintain it regularly can you achieve the best production effect, prolong its working life, and reduce the wear and tear cost. Gemco is a pellet machine manufacture and whosaler, we provide flat die and ring die pellet machine, as well as original spare parts for you to replace. Our engineers can instruct you how to maintain and repaire pellet machine in person. If you have needs or questions, please leave us a message in the form below.
We receive enquiries in English, Español (Spanish), Русский язык (Russian), Français (French) and العربية (Arabic). Our professional team will reply to you within one business day. Please feel free to contact us!